Navigating the 2025 UK Cleaning Compliance Standards
Understanding and implementing the latest regulatory requirements for commercial cleaning
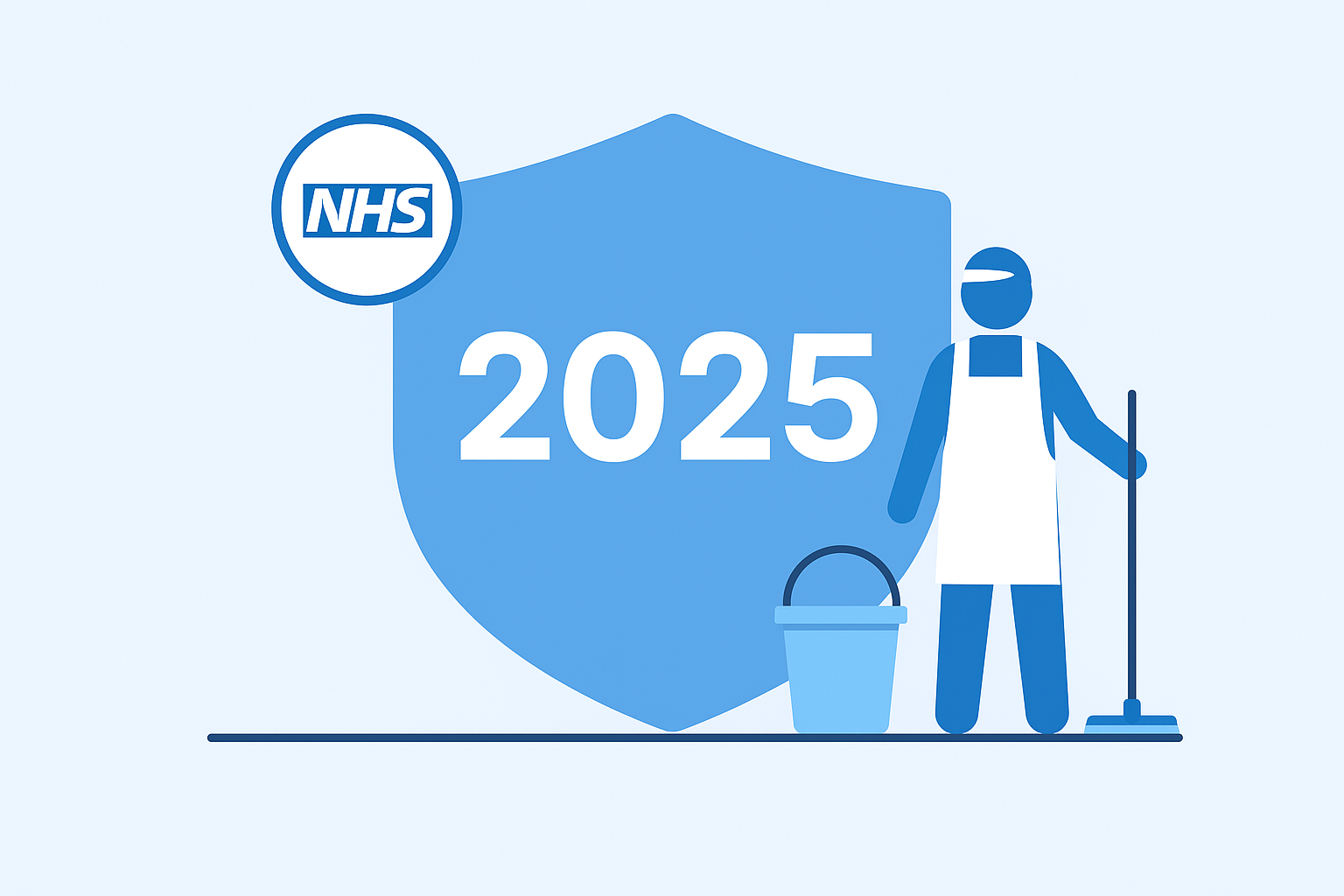
The 2025 update to UK commercial cleaning and workplace hygiene regulations introduces significant changes that affect virtually all business sectors. This article provides a comprehensive overview of the new requirements and practical guidance for achieving compliance.
Key Changes in the 2025 Standards
The 2025 revision represents the most substantial update to UK cleaning compliance frameworks in over a decade, consolidating previously fragmented regulations while introducing new requirements:
Regulatory Area | Previous Framework | 2025 Requirements | Key Implications |
---|---|---|---|
Documentation Requirements | General risk assessments with limited cleaning specificity | Comprehensive Hygiene Management Plans (HMPs) with specific documentation requirements | Organizations must develop formal, auditable cleaning documentation systems |
Staff Training & Certification | General COSHH training for cleaning staff | Enhanced certification requirements with sector-specific modules | Staff require formal training with documented competency verification |
Chemical Management | Basic COSHH compliance | Enhanced product selection criteria and usage tracking requirements | Organizations must maintain detailed chemical usage records and justifications |
Verification Requirements | Visual inspection with limited formal verification | Requirement for objective testing and validation methodologies | Implementation of measurable cleaning quality assessment protocols |
Equipment Standards | Basic functionality and safety requirements | Enhanced efficacy, energy efficiency, and maintenance documentation | More rigorous equipment selection and maintenance record-keeping |
These consolidated standards apply to all commercial facilities, with sector-specific variations for healthcare, food service, hospitality, education, and general office environments.
Implementation Timeline
- January 2025: Standards published
- April 2025: Grace period begins
- October 2025: Staff certification requirements in effect
- January 2026: Full compliance required for all provisions
Hygiene Management Plans: The New Documentation Framework
The cornerstone of the 2025 standards is the requirement for a formal Hygiene Management Plan (HMP), a comprehensive document that outlines an organization's approach to cleaning and hygiene:
Required HMP Components:
- Organizational cleaning policy: A formal statement of principles and commitments
- Facility assessment: Analysis of the facility's specific cleaning needs based on usage, materials, and risk factors
- Cleaning schedules: Detailed timing and frequency of cleaning tasks categorized by area and priority
- Methodology specifications: Precise procedures for cleaning different surfaces and areas
- Chemical inventory: Complete listing of products used, with safety data and selection justifications
- Equipment register: Documentation of all cleaning equipment with maintenance schedules
- Staff training records: Evidence of appropriate training and certification
- Verification protocols: Methods used to confirm effective cleaning implementation
- Corrective action procedures: Processes for addressing identified deficiencies
For organizations with existing documentation systems, our Creating an Effective Workplace Hygiene Policy provides guidance on adapting current protocols to meet the new requirements.
Sector-Specific HMP Requirements:
While the core HMP framework applies across sectors, there are important variations:
Food Service
Additional requirements focused on food contact surfaces and cross-contamination prevention.
Specific Elements:
- • Food surface cleaning validation
- • Allergen control protocols
- • Enhanced pest management integration
Healthcare
Expanded requirements for infection control and specialized area management.
Specific Elements:
- • Enhanced infection control measures
- • Clinical waste handling procedures
- • Pathogen-specific protocols
Educational Settings
Specialized approaches for facilities with varied age groups and activities.
Specific Elements:
- • Age-appropriate cleaning protocols
- • Activity-specific surface management
- • Enhanced frequency for high-touch areas
General Office
Focus on shared spaces and equipment with flexible occupancy considerations.
Specific Elements:
- • Hot-desking hygiene protocols
- • Technology cleaning specifications
- • Common area management
For detailed guidance on sector-specific requirements, our Surface Disinfection Protocols guideline provides tailored recommendations.
Staff Training and Certification Requirements
The 2025 standards introduce substantially expanded training and certification requirements for cleaning personnel:
Core Certification Requirements:
- Basic Cleaning Certification (BCC): Required for all cleaning staff regardless of sector
- Health and Safety Module: Focusing on COSHH and personal protection
- Equipment Operation Certification: Equipment-specific training for relevant staff
- Sector-Specific Modules: Additional certifications based on work environment
- Supervision Certification: Required for anyone overseeing cleaning operations
One of the most significant changes is the requirement for objective competency assessment rather than simply documenting training attendance. This necessitates practical demonstration of skills and knowledge validation.
Certification Options
Organizations can meet certification requirements through several pathways:
- Accredited external training providers: Third-party programs recognized by industry bodies
- Internal certification programs: Organizations can develop in-house programs that meet regulatory requirements if properly documented and validated
- Hybrid approaches: Combining external core certifications with internal specialized training
For assistance developing compliant training programs, our Understanding and Implementing CW UK Hygiene Guidelines course provides comprehensive guidance.
Chemical Management and Product Selection
The 2025 standards significantly expand requirements for cleaning product selection and chemical management:
Key Chemical Management Requirements:
- Product efficacy documentation: Evidence that selected products are effective for their intended applications
- Chemical reduction strategy: Documented approach to minimizing chemical usage while maintaining efficacy
- Product selection justification: Formal documentation explaining why specific products were selected over alternatives
- Usage tracking: Quantitative monitoring of chemical consumption with variance analysis
- Environmental impact assessment: Documentation of environmental considerations in product selection
These requirements align with broader sustainability objectives while ensuring efficacy against emerging pathogen challenges.
For guidance on selecting appropriate products that meet both efficacy and sustainability requirements, refer to our Eco-Friendly Cleaning Supplies article.
Verification and Quality Assurance
Perhaps the most significant shift in the 2025 standards is the requirement for objective cleaning verification rather than sole reliance on visual inspection:
Approved Verification Methodologies:
- ATP testing: Measuring biological residue on surfaces using adenosine triphosphate monitoring
- Fluorescent marking: Using tracers to verify cleaning thoroughness
- Microbial sampling: Direct measurement of microbial presence for high-risk environments
- Quantitative cleaning inspections: Structured assessment protocols with scoring systems
- Environmental monitoring: Measuring airborne particulates and other environmental indicators
The standards require documented verification protocols with specified frequencies, benchmark standards, and corrective action procedures when standards are not met.
For practical guidance on implementing verification systems, see our Surface Testing Methods article.
Common Compliance Pitfall
Many organizations underestimate the documentation requirements for verification systems. The standards require not only the implementation of testing but also formal protocols, benchmark standards specific to the facility, and corrective action procedures tied to verification results.
Equipment Standards and Maintenance
The 2025 standards introduce new requirements for cleaning equipment selection, usage, and maintenance:
Key Equipment Requirements:
- Efficacy documentation: Evidence that selected equipment achieves desired cleaning outcomes
- Maintenance records: Detailed documentation of all maintenance activities
- Calibration schedules: For equipment requiring calibration to maintain performance
- Energy efficiency considerations: Documentation of energy usage optimization
- Cross-contamination prevention: Protocols for equipment cleaning between usage in different areas
The equipment requirements represent a significant expansion from previous standards, which focused primarily on basic safety considerations rather than performance documentation.
For more information on technology-enhanced cleaning equipment that meets the new standards, see our Technology-Enhanced Cleaning Solutions article.
Steps to Compliance: A Practical Approach
Organizations should approach 2025 standards compliance through a structured implementation process:
- Gap analysis: Assess current practices against new requirements to identify deficiencies
- Documentation development: Create or update Hygiene Management Plan documentation
- Training needs assessment: Evaluate staff certification status against new requirements
- Verification system implementation: Develop and deploy objective testing protocols
- Chemical management review: Evaluate product selection and usage tracking
- Equipment evaluation: Assess cleaning equipment against new standards
- Internal audit: Conduct pre-compliance audit to identify remaining gaps
- Corrective action implementation: Address identified deficiencies
The staggered implementation timeline allows organizations to prioritize these steps, focusing first on documentation frameworks and training requirements.
Case Study: Retail Implementation
A UK retail chain with 45 locations developed a systematic approach to 2025 standards compliance:
- Phase 1 (Q1 2025): Gap analysis and documentation framework development
- Phase 2 (Q2 2025): Staff training and certification program implementation
- Phase 3 (Q3 2025): Verification system deployment and chemical management optimization
- Phase 4 (Q4 2025): Equipment evaluation and final compliance verification
This phased approach allowed the organization to distribute resource requirements while ensuring complete compliance by the January 2026 deadline.
Conclusion: Strategic Compliance
While the 2025 standards represent a significant expansion of compliance requirements, they also provide an opportunity to optimize cleaning operations for improved efficacy, efficiency, and sustainability. Organizations that approach compliance strategically will achieve not just regulatory conformance but also enhanced operational benefits.
Key success factors include:
- Taking a systematic approach to implementation
- Viewing documentation as an operational tool rather than just a compliance exercise
- Integrating verification systems into quality improvement processes
- Engaging staff in understanding the purpose behind new requirements
- Leveraging technology to streamline documentation and verification
By approaching the 2025 standards as an opportunity for operational enhancement rather than simply a regulatory burden, organizations can achieve both compliance and improved cleaning outcomes.
Related Articles
Creating an Effective Workplace Hygiene Policy
Step-by-step guidance for developing comprehensive hygiene standards.
Surface Testing Methods
Verification techniques to confirm your cleaning protocols are achieving results.
Choosing Eco-Friendly Cleaning Supplies
A guide to selecting environmentally friendly cleaning products.
Standards Compliance Support
Need help preparing for the 2025 standards? Our compliance consultants can assist with gap analysis and implementation planning.
Request Compliance Support